An unprecedented operation on the hydrogen system
For the first time since the vessel's launch in 2017, the hydrogen tanks on board Energy Observer were removed from their casings for an inspection of the entire high-pressure circuit. This operation kept the team on its toes for over 3 days in Cape Town, South Africa.

With over 6 years of sailing and almost 60,000 nautical miles covered in different latitudes, the boat and her onboard technologies are exposed to harsh environmental conditions, shocks, and extreme temperatures. Wind, sun, salt, and humidity put the equipment to the test, especially the high-pressure circuit. The Energy Observer is fitted with 8 carbon fiber tanks holding a total of 62kg of hydrogen. The high-pressure circuit is made up of hydrogen tanks, piping, connectors, and valves. For the first time, the crew disassembled everything to provide the necessary care and prepare the vessel for the long voyages to come.
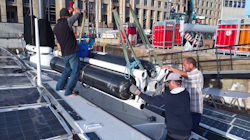
Energy Observer's hydrogen tanks being removed from their casings
A high-flying operation
This operation marked Didier Bouix's return on board. A former engineer with the French Atomic Energy Commission (CEA-Liten), he had supervised the design and installation of the boat's entire energy chain in its early days. In Cape Town, he was able to accompany the technical team in this delicate operation. It was a special moment for Didier, who hadn't been back since 2018. A team from Air Liquide was also on hand to lend its expertise to all the operations carried out and to supply nitrogen for the inerting phase.
“It was hard to get the tanks out because they've been there for so long. It took us 4 hours. They weigh 700 to 800 kg, and the tide made it even more complicated.”
Even before moving the tanks from their casings, it is essential to insert them, i.e. to replace the hydrogen with an inert gas, nitrogen. Inerting allows safe oxygen concentrations to be maintained in the space of the H2 tank, thus reducing the risk of flammability and explosion.
Hydrogen is stored at 350 bars in Energy Observer's tanks. That's equivalent to the pressure that a 3.5 km water column would exert on a given point! Once purged, the team was able to examine the tanks with endoscopic cameras to detect any signs of corrosion or cracks, and check sensors, seals and connectors.
Using an endoscopic camera, Jean Baptiste was able to examine the tanks from the inside and found them to be in good condition, with no cracks or corrosion.
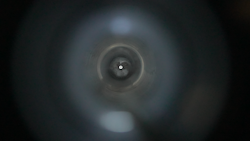
The carbon-fiber tanks, seen from the inside
Connectors and solenoid valves have been replaced. These solenoid valves, screwed to each end of the tank, are used to close the tank. They contain safety valves (which let the gas escape in the event of a problem), a temperature probe and a pressure sensor. It is via this valve that hydrogen filling takes place. The seals and sensors that failed on these valves were replaced.

Jean-Baptiste and Didier examining inside the hydrogen tanks with an endoscopic camera
Once the chambers had been cleaned and the operation completed, the tanks were filled with nitrogen and hydrogen, and a crane was used to bring them back on board.
“For me, it was an opportunity to learn all about inerting. How do you dilute the gas to work safely? And then filling, seeing how our connections are made... I was able to work with Didier Bouix, one of the vessel's fathers. It was really interesting.”

Luc Bourserie et David Champion changent les billes de résine présentes dans les colonnes d’assèchement de l’électrolyseur
The technical team in Cape Town was also able to carry out maintenance on the electrolyser. In particular, they worked on the water dewatering columns. The hydrogen produced by electrolysis, i.e. from water and electricity, has to be dried in these columns, whose balls have been replaced.
Calculations of losses before and after maintenance enabled Didier Bouix to establish that there was very little ageing of the electrolyzer.
These findings are encouraging for the ship's preparation for the long voyages ahead, including a second transatlantic crossing from Namibia to Brazil. The challenge before departure? Produce as much hydrogen as possible, so as to leave with full tanks!
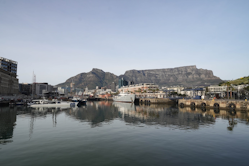
Energy Observer in Cape Town